
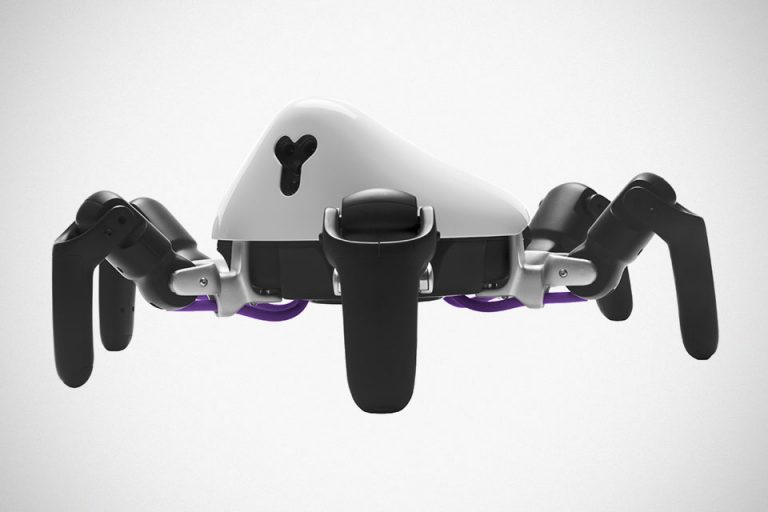
Paretofront of the multi objective optimization of the robot is drawn. In this way, the proper geometrical constraints such aslimitation of universal and spherical joints, and singularity avoidance constraints are considered. Using the multi-objective Bees Algorithm and consideringdynamic and kinematic performance indices in a pre-determined workspace as the objective functions, structure of Hexa parallel robot is optimized. Basedon mass matrix as relation between acceleration vector of the end effecter and torque vector of actuatedjoints, dynamic dexterity index is presented. Inverse of the homogenjacobian-based condition number is considered as an index to evaluate the kinematic dexterity. The Insectbot Hexa DIY Robot Kit is undoubtedly in a bigger body build than its ancestors: 15 larger in size and 20 heavier in weight The Rebounder (see Figure I Connect Hardware 19, buy best diy f550 hexa-rotor air flame 550mm 6-aixs frame kit with universal simple landing skid gear sale online store at wholesale price.

Mass matrix is obtained from calculating thetotal kinetic energy of the manipulator in terms of the actuated joints vector. Jacobian matrix that mapsvelocity from joint space to Cartesian space is developed. In this way, after describing the structure and specifying the geometricalparameters of the robot, inverse kinematic relations of the robot are obtained. M.Uchiyama at the International Symposium on Microsystems, Intelligent Materials and Robots, Sendai, Japan, Sept.In this study, the effects of geometrical parameters of 6-DOF Hexa parallel robot on kinematic, anddynamic performance indices are investigated and its structure is optimized using the intelligent multiobjective Bees Algorithm. We achieved the desired performance, using also a novel approach for friction compensation.Ī newly proposed singularity-consistent path planning and control method has been implemented and tested.īased on the results of our research, we propose a new design for HEXA.The ultimate goal is to increase the maximum speed and achive accleration up to 50 G.Ī special session on parallel robots was organized by prof. Since the HEXA is equipped with DD motors, it was possible to implement compliance control with using a force sensor. (3)Compliance Control Without Force Sensor However, the latter approach is preferable, since it requires less computations than the former. As a result, it was confirmed that both approaches guarantee high accuracy path tracking. We used two approaches based on : a simple dynamic model, and a feedforward velocity component. The acceleration along the Z axis was 27.8G.Īccurate dynamic path tracking has been tested. The HEXA robot achieved one-cycle ADEPT motion performance within 0.465 seconds. The possibility for high speed motion has been evaluated using a bench-mark test motion, which we called ADEPT motion, after the name of the ADEPT robot which has been acknowledged to be the fastest industrial robot. HEXA mechanism / Parallel robot / Closed-loop mechanism / Singularity / Dynamic control / Compliance control PIERROT Francois University of Montpellier, Institute of Information Science, Robotics and MicroeĭAUCHEZ Pierre University of Montpellier, Institute of Information Science, Robotics and Microe NENCHEV Dragomir Tohoku University, Department of Engineering, Associate Professor, 工学部, 助教授 (80270809) KONNO Atsushi University of Tokyo, Department of Engineering, Assistant, 工学部, 助手 (90250688)

TSUMAKI Yuichi Tohoku University, Department of Engineering, Assistant, 工学部, 助手 (50270814) UCHIYAMA Masaru ohoku University, Department of Engineering, Professor, 工学部, 教授 (30125504)

Grant-in-Aid for international Scientific Research
